Weldability in Welding
The American Welding Society defines weldability as,
“the capacity of a metal to be welded under the fabrication conditions imposed into a specific, suitably designed structure and to perform satisfactorily in the intended service.”
In simple terms, the ease with which metals can be fused without producing defects in the finished product is called “weldability”. Many metals and thermoplastics can be welded, but some are easier to weld than others. A material’s weldability is used to determine the welding process and to compare the final weld quality to other materials.
One of the main objectives in welding is to create a joint that is free of cracks and that can withstand the stresses placed on it. When nearly any welding process can be used on a metal and minimal effort is required to produce a sound weld, the metal is said to have “good weldability”. In cases where a welder can choose from only a limited number of welding processes and must carefully prepare the joint and execute the welding procedure to create a strong weld, the metal is considered to have “poor weldability”.
Weldability is considered as ease of accomplishing a satisfactory weld joint and can be in determined from quality of the weld joint, effort and cost required for developing the weld joint. Quality of the weld joint however, can be determined by many factors but the weld must fulfill the service requirements. The characteristics of the metal determining the quality of weld joint includes tendency to cracking, hardening and softening of heat affected zone (HAZ), oxidation, evaporation, structural modification and affinity to gases. While efforts required for producing sound weld joint are determined by the properties of metal system in consideration namely melting point, thermal expansion coefficient, thermal and electrical conductivity, defects inherent in base metal and surface condition. All the factors adversely affecting the weld quality and increasing the efforts (& skill required) for producing a satisfactory weld joint will in turn be decreasing the weldability of metal.
In view of above, it can be said that weldability of metal is not an intrinsic property as it is influenced by,
- All steps related with welding procedure
- Purpose of the weld joints
- Fabrication conditions etc.
Welding of a metal using one process may show poor weldability (like Aluminium welding with SMA welding process) and good weldability when the same metal is welded with some other welding process (Aluminium welding with TIG/MIG). Similarly, a steel weld joint may perform well under normal atmospheric conditions and the same may exhibit very poor toughness and ductility at very low temperature condition. Steps of the welding procedure namely preparation of surface and edge, preheating, welding process, welding parameters, post weld treatment such as relieving the residual stresses, can influence the weldability of metal appreciably. Therefore, weldability of a metal is considered as a relative term.
Factors Affecting Weldability
There are several factors which influence the weldability of metals. Below are some of the most important ones.
- Metallurgy – The science of heating or manipulating metals to produce desired properties or shapes in them.
- Welding Process – There are more than 67 welding processes. Various factors set them apart: how the heat and pressure are applied, how much heat and pressure are used, and the type of equipment employed.
- Joint Design – The combination of the dimensions required for the welded joint and the geometry of the joint.
- Weld Preparation – Weld preparation is a set of techniques to execute prior to welding to prevent defects in the weld. For example, one practice is to clean base metal before welding.
- Melting Point – The temperature that must be reached for a solid substance to melt or fuse. When a metal has a medium melting point, it has better weldability.
- Electrical Resistance – A metal’s opposition, or resistance, to the flow of electrical current. Metals with a high electrical resistance require more heat energy to weld and this makes them have poor weldability.
How to Improve Weldability
The heating and cooling cycles inherent to most forms of welding can create strains and stresses in the weld. They also affect physical, chemical, and metallurgical changes in the metal. When such changes make a metal prone to poor weldability, adjustments can be made to improve the quality of the weld.
- Shielding Gas – Some types of metals, such as copper and aluminum, require a gas to shield them from atmospheric contaminants during welding. Selecting the correct shielding gas for the application in the right quantity can minimize the chance of weld defects.
- Welding Process – Welding charts are available to use as a reference for which process to choose for a metal.
- Filler Metal – Choosing the wrong filler metal can cause defects in the weld, such as cracks and porosity. A good general rule is to select a filler metal that is stronger than the base metal.
- Preheat and Postheat – Brittle metals are prone to cracking during welding. Heating the metal prior to welding and afterward can alleviate this problem.
- Welding Procedure – Weld quality can be dependent on the number of welds, their length, and the size of the weld bead. Several small welds can be more effective than a few large welds.
While all metals can be welded, some fuse more easily than others. However, an understanding of the factors that influence weldability and the practices to improve it can help a welder consistently produce strong and sound welds.
Imperfections in Welds
For steel there are few major failure modes or weld imperfections by which weldability can be measured:
Hydrogen-Induced Cold Cracking
A characteristic feature of high carbon and low alloy steels is that the HAZ immediately adjacent to the weld hardens on welding with an attendant risk of cold (hydrogen) cracking. The weldability of steel, with regard to hydrogen-induced cold cracking, is inversely proportional to the hardenability of the steel, which measures the ease of forming martensite during heat treatment. The hardenability of steel depends on its chemical composition, with greater quantities of carbon and other alloying elements resulting in a higher hardenability and thus a lower weldability. In order to be able to judge alloys made up of many distinct materials, a measure known as the equivalent carbon content is used to compare the relative weldabilities of different alloys by comparing their properties to a plain carbon steel. The effect on weldability of elements like chromium and vanadium, while not as great as carbon, is more significant than that of copper and nickel, for example. As the equivalent carbon content rises, the weldability of the alloy decreases.
High-strength low-alloy steels (HSLA) were developed especially for welding applications during the 1970s, and these generally easy to weld materials have good strength, making them ideal for many welding applications.
Stainless steels, because of their high chromium content, tend to behave differently with respect to weldability than other steels. Austenitic grades of stainless steels tend to be the most weldable, but they are especially susceptible to distortion due to their high coefficient of thermal expansion. Some alloys of this type are prone to cracking and reduced corrosion resistance as well. Hot cracking is possible if the amount of ferrite in the weld is not controlled—to alleviate the problem, an electrode is used that deposits a weld metal containing a small amount of ferrite. Other types of stainless steels, such as ferritic and martensitic stainless steels, are not as easily welded, and must often be preheated and welded with special electrodes.
Lamellar Tearing
Lamellar tearing is a type of welding defect that occurs in rolled steel plates that have been welded together due to shrinkage forces perpendicular to the faces of the plates. Since the 1970s, changes in manufacturing practices limiting the amount of sulfur used have greatly reduced the incidence of this problem.
Lamellar tearing is caused mainly by sulfurous inclusions in the material. Other causes include an excess of hydrogen in the alloy. This defect can be mitigated by keeping the amount of sulfur in the steel alloy below 0.005%. Adding rare earth elements, zirconium, or calcium to the alloy to control the configuration of sulfur inclusions throughout the metal lattice can also mitigate the problem.
Modifying the construction process to use casted or forged parts in place of welded parts can eliminate this problem, as Lamellar tearing only occurs in welded parts.
Porosity
Porosity is formed by entrapment of discrete pockets of gas in the solidifying weld pool. The gas may originate from poor gas shielding, surface contaminants such as rust or grease, or insufficient deoxidants in the parent metal (autogenous weld), electrode or filler wire. A particularly severe form of porosity is ‘wormholes’, caused by gross surface contamination or welding with damp electrodes.
The presence of manganese and silicon in the parent metal, electrode and filler wire is beneficial as they act as deoxidants combining with entrapped air in the weld pool to form slag. Rimming steels with a high oxygen content, can only be welded satisfactorily with a consumable which adds aluminium to the weld pool.
To obtain sound porosity-free welds, the joint area should be cleaned and degreased before welding. Primer coatings should be removed unless considered suitable for welding by that particular process and procedure. When using gas shielded processes, the material surface demands more rigorous cleaning, such as by degreasing, grinding or machining, followed by final degreasing, and the arc must be protected from draughts.
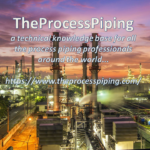
a technical knowledge base for all the process piping professionals around the world…