Introduction to Pipe Support
A pipe support is a designed element that transfer the load from a pipe to the supporting structures. The load includes the weight of the pipe, the content that the pipe carries, all the pipe fittings attached to pipe, and the pipe covering such as insulation. The four main functions of a pipe support are to anchor, guide, absorb shock, and support a specified load. Pipe supports used in high or low temperature applications may also contain insulation materials. The overall design configuration of a pipe support assembly is dependent on the loading / operating conditions and pipe support location.
Type of Loads
Primary Loads
Primary loads are typically steady or sustained types of loads such as gravitational forces acting on the pipe such as weight of pipe and fluid, internal fluid pressure, external pressure on pipe, forces due to relief or blow down, pressure waves generated due to water/steam hammer effects, wind and seismic loads.
Sustained Loads
-
Dead Weight
It is the self weight of pipe including contained fluid, weight of pipe fittings & other inline components (say flanges, valves, insulation etc.). This type of load act throughout the life cycle of pipe. These loads cause bending, and the bending moment is related to normal and shear stresses. In horizontal pipes, this load is taken care by placing pipe support on regular span to avoid sagging of pipe. In vertical pipes, this load is taken care by placing adequate load taking support in the horizontal portion just before/after vertical portion or lug support in the vertical portion.
-
Internal / External Pressure
A pipe used for transporting fluid would be under internal or external pressure load. A pipe with high pressure fluid is under net internal pressure whereas pipe with vacuum conditions or jacketed pipe covering may be under net external pressure. Internal or external pressure induces stresses in the axial as well as circumferential (Hoop Stress) directions. The pressure also induces stresses in the radial direction, but these are often neglected. This type of load is usually taken care during the selection of material for pipe. Pipe material must withstand these stresses at the prescribed temperature and pressure conditions.
Occasional Loads
-
Wind Load
Piping which are located outdoors and above a certain elevation are exposed to wind and will be designed to withstand the maximum wind velocity expected during the plant operating life. Wind pressure for various elevations is used to calculate wind force.
-
Seismic Load
Seismic load is one of the basic concepts of earthquake engineering which means application of an earthquake-generated agitation to a structure. It happens at contact surfaces of a structure either with the ground, or with adjacent structures, or with gravity waves from tsunami.
-
Water Hammer
Water hammer is a pressure surge or wave caused when a fluid (usually a liquid but sometimes also a gas) in motion is forced to stop or change direction suddenly (momentum change). Water hammer commonly occurs when a valve closes suddenly at an end of a pipeline system, and a pressure wave propagates in the pipe. It’s also called hydraulic shock.
For more on Water Hammer, check out Water Hammer in Process Plant
-
Steam Hammer
Steam hammer, the pressure surge generated by transient flow of super-heated or saturated steam in a steam-line due to sudden stop valve closures is considered as an occasional load. Though the flow is transient, for the purpose of piping stress analysis, only the unbalanced force along the pipe segment tending to induce piping vibration is calculated and applied on the piping model as static equivalent force.
-
Safety Valve Reaction Force
Reaction forces from relief valve discharge is considered as an occasional load. The reaction force due to steady state flow following the opening of safety relief valve in an open discharge installation can be calculated in accordance with ASME B31.1 Appendix II and applied on the piping model as static equivalent force.
For more on Pressure Safety Valve, check out Introduction to Pressure Safety Valve
Secondary Loads
Secondary loads are caused by displacement of some kind. For example, the pipe connected to a storage tank may be under load if the tank nozzle to which it is connected moves down due to tank settlement. Similarly, pipe connected to a vessel is pulled upwards because the vessel nozzle moves up due to vessel expansion. Also, a pipe may vibrate due to vibrations in the rotating equipment it is attached to.
A pipe may experience expansion or contraction once it is subjected to temperatures higher or lower respectively as compared to temperature at which it was assembled. The secondary loads are often cyclic but not always.For example load due to tank settlement is not cyclic. The load due to vessel nozzle movement during operation is cyclic because the displacement is withdrawn during shut-down and resurfaces again after fresh start-up.
Types of Pipe Support
Rigid Support
Rigid supports are used to restrict pipe movement in certain direction(s) without any or limited flexibility in that direction. Main function of a rigid support can be:
-
Anchor or 3 Dimensional Stop
In this type of support arrangement, pipe is fixed with reference to the supporting structures. Movement in any direction is not allowed. This can be achieved by welding or bolting the support with supporting structure.
-
Rest or Sliding Support
In this type of support arrangement, pipe is fixed with reference to vertical downward direction. Movement in downward vertical direction, mainly due to the weight of pipe and containing fluid, is not allowed. This support is sometimes also referred as sliding support.
-
Guide
In this type of support arrangement, pipe is fixed with reference of directions other then the direction in which weight of pipe and containing fluid is acting. Limited flexibility can be provided with the provision of guide gap (gap between pipe outer surface and guide plate inner surface).
-
Both Rest & Guide
In this type of support arrangement, pipe is fixed with reference to vertical downward direction along-with any or all the guide directions.
Spring Support
Spring supports are used to support a load and allow simultaneous movement. Spring supports use helical coil compression springs (to accommodate loads and associated pipe movements due to thermal expansions). The critical component in both the type of supports are Helical Coil Compression springs. They are broadly classified into,
-
Variables Effort support
Variable effort supports also known as variable hangers or variables are used to support pipe lines subjected to moderate (approximately up to 50mm) vertical thermal movements. Variable effort supports are used to support the weight of pipe work or equipment along with weight of fluids while allowing certain quantum of movement with respect to the structure supporting it. Hot load is the working load of the support in the “Hot” condition i.e. when the pipe has traveled from the cold condition to the hot or working condition. Load Variation (LV) or Percentage variation =[(Hot Load-Cold Load) x 100]/Hot Load or [(Travel x Spring Rate) x 100]/Hot Load. Normally MSS-SP58 specifies max Load Variation ( popularly called LV) as 25%.
-
Constant effort support
Constant effort supports are used to support pipe lines subjected to large vertical movements typically 150 mm or 250 mm. For pipes which are critical to the performance of the system or so called critical piping where no residual stresses are to be transferred to the pipe it is a common practice to use CES. In a constant effort support the load remains constant when the pipe moves from its cold position to the hot position. Thus irrespective of travel the load remains constant over the complete range of movement. Therefore it is called a constant load hanger. Compared to a variable load hanger where with movement the load varies & the hot load & cold load are two different values governed by the travel & spring constant. A CES unit does not have any spring rate.
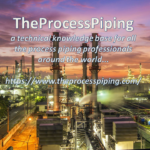
a technical knowledge base for all the process piping professionals around the world…
Valery, the man built the plants before the creation of finite elements theory. Codes have been developed to rule these issues. We are engineers, not physicists. A simplified theory with a safety margin is better than a precise but too time-consuming one. A theory based on experience results is also acceptable even if not supported by theoretical calculations in its entirety. So We have code by rules (B31.etc) that are not “illegal” and also supports standard that have been always used and only now analyzed with the new calculation methods. So We can consider a Pipe as a Beam, the important is to know when a shell problem can arise, but codes help to avoid them.
The application of the theory of girder finite elements to the stress simulations of pipelines is “illegal”.
The hypothesis of FLAT sections and the Saint-Venant principle are valid only for long rods of a LIMITED profile, i.e. having transverse dimensions of ONE order!
For thin-walled beams, when one transverse dimension is much larger than the other, estimates of the relative orders of magnitude of the normal and tangential stresses cease to be valid, the hypothesis of flat sections loses force and the Saint Venant principle becomes unacceptable.
Pipe is not a beam element
Pipe is a thin cylindrical shell
Therefore, for almost all cases – the pipeline should be considered as a shell construction
In the process of loading the pipeline, the cross section ceases to be perfectly round – the curvature of the pipeline changes, both radially and in the longitudinal direction – this can not be taken into account by the theory of beam finite elements.
The beam theory of finite elements excludes the possibility of REAL simulation of the contact of pipelines with supports.
And since in the process of loading the area of contacts and their location change – the beam theory of finite elements can not give REAL values of stresses that arise in contacts.
You are mistaken in saying that the pipelines have small deformations.
Almost always – pipelines have large deformations and almost always pipelines have geometric nonlinearity.
Applying the theory of beam finite elements it is impossible to obtain distribution of stress at the intersection / conjugation of pipes, as well as at the intersection / junction of pipes with reservoirs.
Applying the theory of beam finite elements it is impossible to correctly define the boundary conditions that simulate the supports – since the boundary conditions are set to points located on the axis of symmetry of the pipeline.
In fact, the support of the pipeline to the supports occurs along the outer surface of the pipeline – thus the “error” in setting the boundary conditions will be 0.5 the radius of the pipeline.
The consequence of this is an incorrect calculation of the forces , bending and twisting moments => incorrect distribution of strain/stress in pipe.